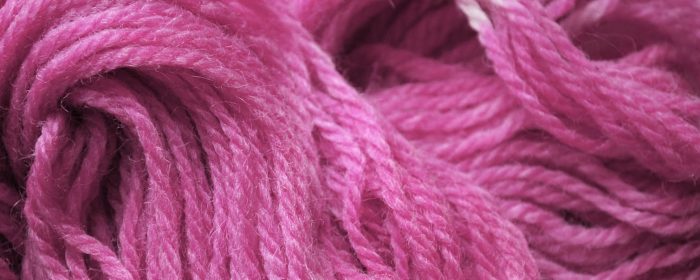
What Is The Chenille Yarn?
For beautiful appearance and softness, chenille yarn has become the choice of fabric designers for many items. The softness and sheen of chenille improves the appearance and hand of thousands of everyday items, including sweaters, outerwear fabrics, upholstery and curtain fabrics, throws and blankets, and area rugs.
Chenille is a pile yarn that has been produced commercially since the 1970s. In the early years, the machinery used for commercial production resulted in chenille with variable characteristics. Modern machinery was introduced in Europe and North America in the early 1990s, and today’s chenille is a reliable and beautiful yarn that is gaining in popularity.
CIMA is dedicated to improving industry manufacturing practices through education, to assure easier use of this beautiful yarn. Chenille is a difficult yarn to manufacture, requiring great care in production. Due to the nature of chenille’s pile direction, pile completeness (or lack of missing pile), and strength-to-bulk relationship, great care must be taken in converting chenille into final articles. The following information is designed to give an understanding of the chenille manufacturing process and the technical specifications necessary to properly convert chenille yarn into finished goods.
THE NATURE OF CHENILLE YARN: Chenille yarn consists of short lengths of spun yarn or filament that are held together by two ends of highly twisted fine strong yarn. The short lengths are called the pile and the highly twisted yarns are called the core.
Chenille yarn can be made from many different types of fibers and yarns. Most common are cotton, viscose (rayon), acrylic, and polypropylene (olefin). Chenille yarn can be made in many different sizes, ranging from as heavy as Nm 0.2 to as fine as Nm 12.0.
THE MANUFACTURING PROCESS: Chenille yarn is manufactured on a machine that is designed to bring the pile yarns and core yarns together. During manufacture, the pile yarns are wrapped around a short stem of polished metal, called a caliper, through which a blade passes to cut the pile yarns into short lengths. The core yarns are pressed onto the short lengths with a rotating metal wheel.
The resulting yarn is then fed onto a traditional ring twisting take up mechanism. In the twisting process, the two ends of core yarn twist and trap the short ends of pile between the core yarns. The size of the caliper determines the diameter of the resulting yarn. The size and number of the pile yarns and how much of them are fed onto the core determines the count of the yarn.
CHENILLE QUALITY TOLERANCES: The nature of the chenille process results in a wider range of yield and twist variation compared to other yarn manufacturing processes. The yield and twist tolerances are as follows:
INTERNATIONAL SPECIFICATION FOR CHENILLE COUNT AND TWIST TOLERANCES
Sample Size | 1 | 5 | 10 | 25 | 100 |
Count/Yield (% ±) | 20.0 | 10.0 | 6.0 | 4.0 | 2.0 |
Twist (% ±) | 20.0 | 10.0 | 6.0 | 4.0 | 2.0 |
CHENILLE YARN MANUFACTURE: Chenille is manufactured in a two step process. Step one is the manufacture of the chenille onto a chenille bobbin, and step two is the rewinding of the chenille onto a cone or dye tube. An electronic clearer is located in the yarn path of step two to detect lengths of yarn that have pile missing. When the electronic clearer detects a section of missing pile greater than the minimum setting specified (usually 3 mm), a cutter is electronically activated. The yarn is cut, and the winder operator then pulls the yarn back and cuts out the missing pile section, reties the yarn, and continues winding the package. The electronic clearer devices are almost 100% effective.
ELECTRONIC CLEARING OF MISSING PILE: It is important to verify with your chenille supplier that the chenille yarn has been electronically cleared to remove the missing pile.
KNOTS AND SPLICES: Knotting or splicing chenille must be done carefully to avoid defects in the items that use chenille yarn. Simply tying a knot in the chenille yarn itself creates such a defect, so there are two alternative methods for “tying” the chenille yarn.
Method one is a core knot. This is made by stripping back the pile of both ends of the chenille sufficiently so that it is possible to tie a double square knot in the core yarns. Care has to be taken to hold the twist in the yarn ends where the pile starts. Once the double square knot is tied, the ends are clipped close to the small knot. The pile ends are then pushed over the knot. Method two uses a splice. To create the splice, the two ends of chenille are overlapped 1 ½ to 2 inches and a mechanical wrap-around splicing device applies the wrap yarn. The wrap yarn can be either a fine monofilament nylon or a very fine yarn of the same fiber as the chenille pile.
PILE DIRECTION: The chenille manufacturing process creates pile that lies in one direction. When woven into a fabric, chenille reflects light differently when viewed from different directions. This is known as the “reflection effect,” and it is one of the unique and desirable characteristics of chenille goods. Because of this, strict control of the pile direction must be maintained during both the step of manufacturing the chenille and also all subsequent processes required to convert the chenille into a finished article.
It is not possible accurately to visually evaluate the direction of natural or dyed chenille yarn in its yarn form. Weaving the chenille yarn into a solid test fabric is the only way of detecting the true direction of a yarn. The appearance of a “V” or an inverted “V” in the pile can reflect other characteristics of the chenille yarn other than direction. Following step one of manufacturing, the yarn has direction one. After the winding process in step two, the yarn has direction two. The chenille yarn producer has taken all the necessary steps to ensure that the chenille yarn is all in the same direction when it is shipped to the user.
The chenille yarn user must take care to maintain the same pile direction throughout manufacturing. For example, with yarn sold on dye tubes and coned after dying, if rewinding is necessary (as in the case of cross-wound yarn or packages that are too hard or soft), the yarn must be rewound TWICE so that all the yarn remains in the original pile direction. If this rule is not strictly observed, streaks will result in the final fabric.
FIBER COMPOSITION: Fiber composition is quoted on the chenille yarn supplier’s invoice and on the yarn cone. If the yarn is put up on a dye carrier, labels are not used on the yarn carrier to avoid possible interference during the dyeing process.